EDM (WIRE / CONVENTIONAL)
The Importance of EDM in an Ever-Changing Industrial Landscape
Today’s industrial landscape is constantly changing and companies need flexible, reliable tool & die manufacturing solutions to stay ahead of the curve and deliver high-quality products to their customers. Header’s long-standing dedication to state-of-the-art tool & die manufacturing technology combined with the insight and skill of our expert technicians help companies like yours experience the unparalleled quality of Electrical Discharge Machining (EDM).
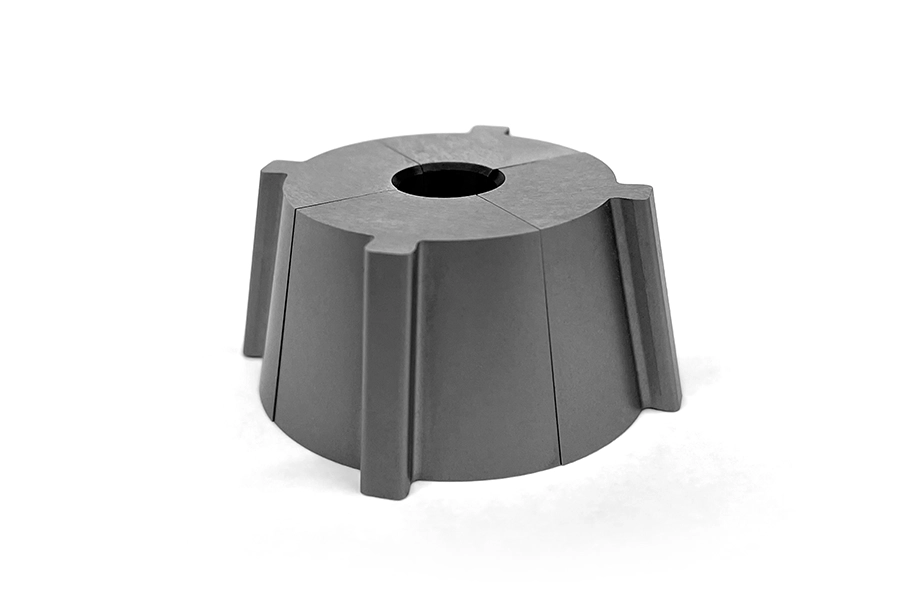
Electrical Discharge Machining (EDM) is an advanced technique that uses electrical discharges to machine precise detailed cuts. With the ability to consistently replicate customized machining, EDM manufacturing is the ideal solution for parts with precise tolerances, unique features, or challenging materials.
Header houses three types of EDM manufacturing technologies — WIRE EDM, CONVENTIONAL/SINKER EDM, and small hole drilling EDM — to offer customers the most ideal machining needs for specific applications.
Wire EDM manufacturing uses an electrical discharge between the wire and the workpiece to achieve precise, detailed cuts. A spark is transmitted between a single strand of wire and the workpiece where it jumps what’s referred to as the spark gap to burn away material from the workpiece. In order to control the sparking process and prevent an electrical short, dielectric, non-conductive fluid is used to either flush or submerge the entire process. The continuous flow of dielectric fluid also removes the eroded waste material.
Wire EDM is used primarily for cutting shapes through assemblies and inserts. This means a predrill hole is necessary to feed the wire through the workpiece. Wire EDM manufacturing is used only when the necessary machining cuts through the entire workpiece.
Wire EDM offers several benefits and advantages compared with other methods of machining, and, more specifically, the other methods of EDM manufacturing. Generally speaking, wire EDM adds value to the machining process by eliminating the need for tooling and producing accurate part prototype runs with shorter lead times. In addition, wire EDM allows for the accurate replication of intricate parts with no deflection.
Other wire EDM benefits include:
- Precise, burr-free cuts within +/- .0003”
- Internal corner cuts with nearly square edges
- Capability to cut long tapers
- Machining of pieces up to 12″
- Machining after heat treatment to ensure dimensional accuracy is not affected by heat distortion
Conventional/Sinker EDM – also known as die-sinking EDM – utilizes an electrode that is machined to the shape or form that is specified in the finish part. These electrodes are machined from either graphite or copper.
Typical Conventional/Sinker EDM applications are performed with the workpiece submerged in dielectric fluid. This fluid serves various purposes such as providing cooling for heat-impacted zones and preventing damage to the workpiece, as well as acting as a conductor between the electrode and the workpiece. The superior level of precision achieved through Conventional/Sinker EDM – which is not attainable through alternative machining methods – has established it as the standard method for machining production prototypes across a variety of industry applications.
Our RAM EDM electrodes are created using a 5-axis high speed machining process. All the desired features are machined on to the electrodes; the end result does not require any secondary processes like blending or hand-scraping.
Conventional/Sinker EDM provides a number of benefits and advantages compared to more traditional machining methods. While enhanced levels of precision lead the way in terms of advantages, Conventinal/Sinker EDM also offers increased consistency, repeatability, and efficiency in machining materials to very close tolerances. In addition, it allows for fine finishing control without compromising structural integrity.
Other important benefits Conventional/Sinker EDM provides include:
- A wide range of shapes and sizes inside blind cavities
- Rapid set-up time
- Internal splines, blind keyways, and molds
- Capacity for complex shapes compared with conventional cutting tools
- Machining of delicate sections or weak materials due to no contact between tool and workpiece
Small hole drilling EDM — also known as Hole Popper EDM — utilizes a brass or copper electrode tube that rotates in a stream of distilled water to flush away the eroded material created during machining. Hole Popper EDM allows for extremely precise machining with the capacity for 0.3mm to 6.1mm diameter holes to be drilled through a 10mm piece of soft or hardened steel.
The high degree of precision and rapid processing time of Hole Popper EDM makes it ideal for a number of industrial applications, and this method of EDM also provides a number of important benefits for manufacturers in overcoming many of today’s common challenges, including:
- Quick job turnaround for a significant reduction in lead times
- Decreased set-up time due to minimal tooling work
- Capacity for drilling into hardened materials, which eliminates the change of size fluctuation caused by heat treating
Our EDM department can easily manufacture a variety of parts ranging in size from .040” in diameter to over 20" in diameter. In addition, our cutting-edge EDM manufacturing processes provide surface finish control without compromising structural integrity for a durable final product that is engineered for a long service life.
What makes Header a unique tool & die manufacturer is our dedication to blending old-world craftsmanship with the latest machining technology to tackle any challenge or overcome any obstacle. In partnering with Header for your EDM manufacturing needs, you’ll be able to adapt and respond to wherever today’s manufacturing markets take you.
CONTACT HEADER DIE & TOOL
See what we can do for you today!